Description:
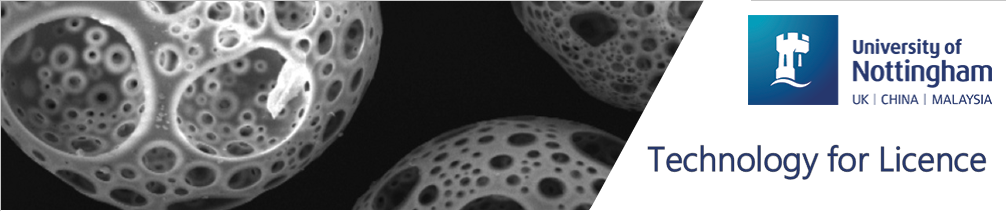
Porous Glass Microspheres
A tailored, single-stage and scalable manufacturing process
In brief
Porous glass microspheres (MS) are produced via a novel flame spheroidisation process, enabling precise tailoring of MS porosity, size, chemistry and other variables to address a
wide range of potential applications.
Compared to other manufacturing techniques, this single-stage process is: efficient, less time-consuming and energy intensive, scalable, and offers better control over pore size,
interconnected porosity and morphology.
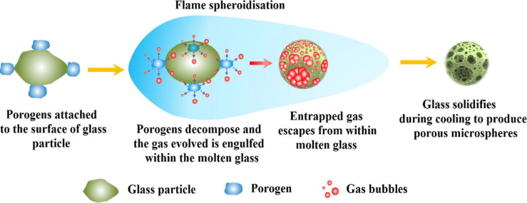
Fig 1: Schematic representation of the proposed mechanism for manufacturing porous glass microspheres
via the flame spheroidisation process.
Background
Microspheres exhibit greater advantages over irregular-shaped particles, with an improvement in flow properties and the porous or hollow structure. Porous microspheres can be
loaded with active or functional entities. They have a relatively large surface area and allow for the encapsulation of components, leading to a wide range of uses, from adhesive
additives to drug delivery or energy storage.
Key features
This technology is a novel flame spheroidisation process to manufacture highly porous glass microspheres.
Key features are:
• Particles produced are of spherical morphology
• The production technique is eminently scalable with the current lab-scale production method at 1–3 kg/h.
• Facile production process amenable to be transferred to GMP standards
Demonstrated in bone regeneration
Research has proven the effectiveness of injectable pastes of porous calcium phosphate glass microspheres in tissue engineering and bone regeneration. Glass microsphere
formulations with 40 mg/mL xanthan gum displayed optimal flow characteristics and were readily injectable via a syringe-needle system (3–20 mL, 18G and 14G needles), proving
their potential as a cell (or other biologics) delivery vehicle.
Tailorable properties
• Size: ranging from 60–350 microns diameter
• Level of porosity: from <5% up to >80%
• Degradation rates: can be controlled from days, weeks up to months.
• Base material: phosphates, silicates, borates and glass ceramics – the main types of bioactive glasses
Applications in engineering, biotechnology and healthcare
Applications for this novel fabrication process have been identified in: medical devices, bone regeneration, resorbable implants, separation science, osteoplasty, bone surgery,
joint surgery, hip revisions, spine surgery, spinal fusion, osteo-conductivity, orthopaedic surgery, dentistry, bone fixation, filtration and fillers.
We are interested in licensing or collaborations related to potential areas of application.
Small samples for assessment can be supplied by agreement.
IP
Patent protected - WO2016027110, EP3183224
Enquiries
Peter McLeod - Licensing Executive
peter.mcleod@nottingham.ac.uk
Tel: +44 (0)115 74 85507
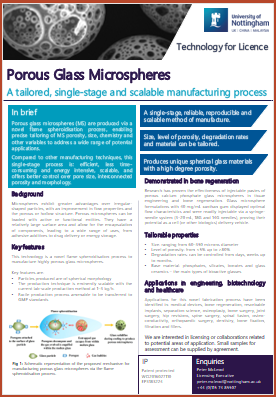
Download pdf